As hotels reopen after a lengthy pandemic-driven shutdown, they are challenged with managing the status of linens that were little used for months or a year. The hotels need to guarantee the linens are available, serviced and returned to linen closets immediately, without the distraction of manual counting. A hotel in United Kingdom reopened its doors to approximately 50 percent capacity, and it is using data provided by passive UHD RFID laundry tag reads to view its available inventory of bedsheets, towels and other laundered assets automatically.
The hotel contains 165 rooms and has been in operation for 20 years. As it resumes services, it will be using fresh linens, and it plans to employ the laundry service’s RFID data to view automated updates of the inventory it has onsite.
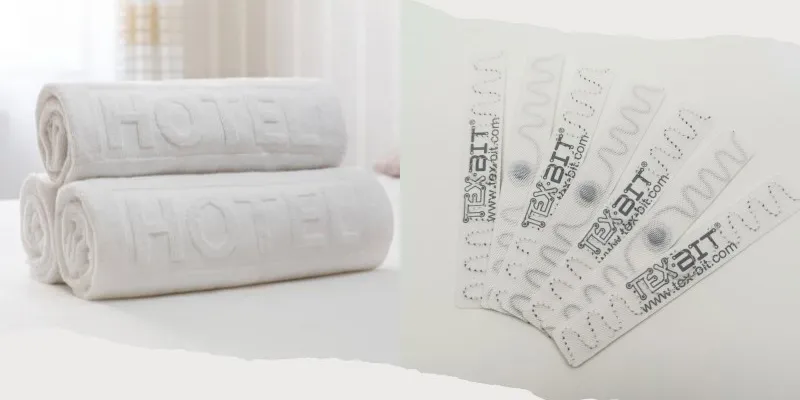
Hotel Linen Management without RFID Laundry Tag
The hotel’s long-term plan is to provide real-time data from its linen closets regarding which textile assets require reordering. Initially, however, it will benefit from data at its laundering facilities, to ensure the necessary clean linens are always available for returning guests. It should be very beneficial for our housekeeping. Prior to all this, it was all very manual. We counted the sheets and counted the linens, so it was really unproductive and time-consuming.
RFID Laundry Tag for Hospitality and Hotel Linen RFID Management
Now, as the hotel reopens following a lengthy COVID-19 shutdown, it intends to be more efficient. With the RFID linen transponders on every linen item the hotel uses, The Hotel can access data in the cloud-based software about linen stocks onsite, and it can then place orders as needed. The RFID technology will save labor and ultimately make the hotel team more productive. They will spend fewer hours counting, and more hours servicing rooms and serving our clientele.
A linen rental company owns and maintains the linens leased by its customers, which launched 34 years ago, was growing exponentially in recent years, before the pandemic hit. It served hotels representing a total of 570 rooms in 2017, but by 2019 it had grown to 2,895 hotel rooms. That equates to a growth of 507 percent within three years.
As the company grew, it has invested in equipment to automate processes and improve efficiency. He saw the advantage of employing RFID to automatically identify each of thousands of fast-moving linens, whether clean or soiled—even those packed in rolling cages or bags. When you’ve got just 500 bedrooms, you’re always relying on your staff of people. Retrofitting its products for customers was manageable, when its clientele was still relatively small.
The big companies have been slower to adopt such technology, in part because many that process high volumes of goods simply do not count them at all. Without a way to automate the identification of items large and small, companies often must write off a percentage of goods annually that end up missing. For the company, that was not a tenable strategy, either for its own purposes or for its customers who count on having clean linens onsite.
So the company began experimenting with the technology around 2016. It acquired an RFID solution from laundry service software firm, which consists of RFID tags sewn onto linens, along with reader portals. The system comes with cloud-based software to manage the collected read data as tagged items are rolled in cages past the RFID reader antennas, or as handheld or desktop readers capture tag IDs.
The linen rental company sews the tags onto its own linens in-house, and it has tagged 271,400 items thus far. RFID technology helps the company automated counting of items being received and then laundered and shipped helps the company prevent errors or out-of-stock events.
First, goods are received at the laundering facility as the van carrying them enters a dedicated entrance. They are wheeled through a tunnel reader, where tag IDs are captured and transmitted to the software to update each tagged item’s status. The linens then sit in a holding area. A ceiling-mounted RFID reader at that location also captures the tag IDs of all goods dwelling there. The software includes a module enabling users to view the status of each item so that the linen textile supplier can obtain an update about a specific customer’s goods, or a specific item.
The goods are sorted manually after being received and bagged. When a bag reaches a weight of 60 kilograms (132 pounds), the facility’s robotics system lifts it into a lane leading to the laundering services. After being washed and folded, the linens are moved to another section of the facility, where staff members use a desktop UHF RFID reader. They can view orders on a PC running the software, while the reader captures the tag IDs of all clean items being packed to fulfill a customer’s order. Drivers could also use handhelds to capture data indicating what has been loaded into their vehicle.
The use of RFID will serve a value in helping companies resume their operations after closure or slowdown. The technology will help us to scale a lot quicker, by tracking items that come in for laundering after sitting for months in storage without being used, for instance. During the lockdown, the company visited its customers’ facilities and updated their inventory data’s status, known as its “aging profile.” In that way, the system knows which goods are not being used and thus are not subject to the usual wear and tear.
Going forward, it’s going to be really busy, and RFID will help. Data is power—if you can look at your screen and know what’s going on, that’s a benefit for us and our customers. RFID is going to help us scale up much more quickly. The solution has not only made counting more efficient and accurate, but has eliminated calls from customers seeking updates about the inventory they may or may not have onsite. In the past, such calls had required subsequent manual counting.
With a proven RFID Laundry Tag Manufacturer
RFID technology delivers automated tracking and inventory management for hotels, hospitals, and other industrial linen operators. Durable UHF RFID tags survive repeated high-temperature laundry cycles while providing each item with unique identification. However, not all RFID laundry tags have stable performance. Choosing an experienced RFID linen tag partner ensures reliable performance in demanding environments.
TEX-BIT, as a professional RFID laundry tag manufacturer with millions of RFID linen tags working all over the world. For industrial laundries, we’ve spent years focused specifically on linen tracking. Through rigorous in-house design, testing, and production improvement, here are the key advantages we offer:
1, Own development and design of a wide range of RFID products, the entire RFID industry know-how to various aspects of technology.
2, With strict product design and production management, to ensure the operation of the customer system.
3, Years of tracking and testing of the fabric industry, designed for the most challenging laundry environment, not afraid of any challenge to the test.
4, A variety of linear, a variety of materials constantly tested, the formation of a full range of laundry products.
5, In the client’s test reports show that not worse than other similar products.